cactusddd
其实论文百度中搜索一下,也是有范文的,你可以自己找一下,没有必要等别人发给你。自己试试吧,还节省时间 KJKlrrcTmskmQh 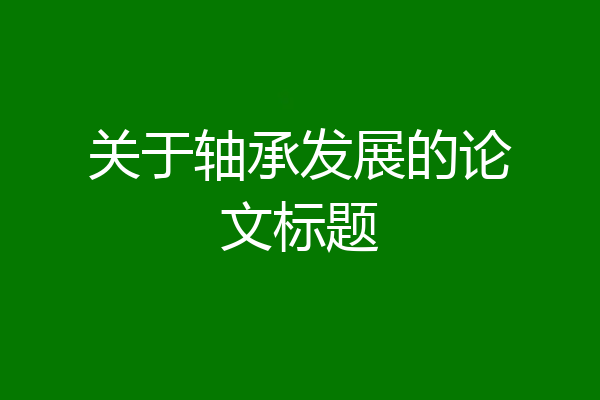
滚动轴承套圈制造技术1 锻造加工 轴承生产中,套圈毛坯质量的好坏,生产率的高低,都将对轴承产品的质量、性能、寿命以及企业的经济效益产生重要影响。毛坯留量的大小(包括毛坯的成型方式)决定轴承材料利用率,而毛坯尺寸分散度和几何形状精度差则是造成废品率高、不能自动化生产的主要原因。套圈毛坯有锻件、冷挤压、温挤压、棒料和管料等,锻件约占毛坯总数的85%左右,套圈毛坯锻造的劳动量约占轴承加工总劳动量的10%-15%。目前中小型套圈用锻件来加工的比重有加大趋势。 目前,国内套圈锻造以热锻为主,以压力机锻造-辗扩成型生产线为主。锻造加热采用煤、油和电加热。加热火耗损失为1%-3%,表面脱碳层深度为3-4mm,材料利用率为40%-50%。20世纪八十年代,有些轴承企业在小型轴承套圈上推广了冷挤压工艺,对外径80-130mm的套圈采用温挤压工艺,外径小于80mm的套圈采用冷辗工艺(目前行业上以扩大到150mm一下),材料利用率达到60%以上。 我国相继引进了16条高速镦段机生产线,推动了轴承行业锻造水平的技术进步,加快了毛坯专业化生产过程。高速镦锻工艺目前已成为国际上轴承套圈锻造的主要工艺,其采用感应加热至始锻温度,在高速顿锻机上完成切料、镦饼、成形和分离等工序,使用于大批量生产。高速镦锻工艺生产效率高,锻件尺寸精度高,表面质量好,能降低留量,提高材料利用率。 综上所述,我国轴承锻造毛坯发展方向应为:进行专业化经济规模生产,便于采用国际先进技术,如高速镦锻工艺、精密冷辗扩工艺、控制气氛等球化退火工艺等,采用先进工艺可以将目前轴承行业40%的材料利用率提高至54%-60%,经济效益可观。2 车削加工 车削加工是金属切削加工的重要组成部分之一,在机械制造业中应用最为广泛,占有十分突出的地位。目前,我国中、小型轴承套圈大多采用多刀半自动、全自动车床对锻件进行车削加工。加工方式有机群分散工序和集中工序。 在国外,目前套圈车削加工采用的有集中工序,也有分散工序法。集中工序法多用于结构形状复杂的零件,采用数控车床一次装夹定位,机床配备有刀具库,加工中,各工序通过精确地程序设计完成,产品精度受人为因素影响较小。分散工序法多用于大批量单品种的加工,采用自动化连线的方式加工。广泛使用的刀具是硬质合金涂层机夹刀片,其切削速度达到140-250m/min,生产效率明显高于国内。采用了先进的毛坯加工技术,因此国外毛坯留量小,尺寸分散度小,车削加工一般为单循环完成,有效地缩短了加工周期。 因此,发展能实现强力切削、刚性好的套圈车削专用车床,发展加工质量好、效率高的微机控制和自动控制车床,以及适合大批量单品种生产的自动化车削生产线,是车加工的发展方向。此外,发展硬质合金机夹可转位刀具、表面涂层刀具、金属陶瓷刀具等高效刀具,以及实现自动更换刀片、自带断屑装置等刀具监控系统,也是车加工研究的一个方向。3 磨削、超精加工 轴承生产中,磨削加工劳动量约占总劳动量的60%,所用磨床数量也占全部金属切削机床数量的60%左右。磨削加工成本占整个轴承生产成本的15%以上,因此,磨削加工是轴承生产的关键工序。 目前国内轴承行业的一般磨削、超精工艺过称为:外圈:平面磨削- 外径磨削-沟(滚)道磨削-沟(滚)道超精内圈:平面磨削-内外径磨削-内径磨削-沟(滚)道磨削-沟(滚)道超精 在实际生产中,视产品精度要求在以上过程中增加附加回火工序,或对各表面进行二、三次循环加工。磨削过程多采用单机加工,较好的企业建有自动化生产线。改革开放以来,我国轴承行业有了较快发展,特别是磨超生产工艺有了较大改进,如沟道切入磨代替了摆头磨,双端面磨、宽无心外圆磨削、沟(滚)道超精工艺及支沟磨沟工艺已普遍应用,告诉磨削也开始应用。但是相对国外轴承磨超加工,我们还存在较大差距,在国外先进的轴承制造企业,端面、外径磨削采用CNC数控自动送料,在线自动测量、自动补偿,磨削速度达45m/s。沟道、内径磨削已全部采用CNC数控机床,生产过程实现全线自动化,全部工序由计算机集中控制,所有工艺参数和生产节拍严格按照图纸设计控制,砂轮线速度达到60m/s。SKF磨加工工序的内沟磨削速度已达到120m/s。特别是使用性能优良的CBN砂轮,使生产效率明显提高。 轴承套圈磨削的发展趋势,集中体现在以下几个方面: (1) 对轴承磨床,进一步实现单机自动化,确保实现高速磨削、自动测量,使其能直接进入自动线并可靠工作。 (2) 磨加工生产要有步骤、有组织地发展自动化生产线。目前,世界主要轴承公司磨加工自动化程度很高,大批量产品均采用自动线组织生产,而采用自动化生产线,投资少、见效快,易于稳定生产。 (3) 发展相关技术。如各种新型家具、高速砂轮、超精油石、冷却液及润滑油、数控元器件等,不断提高工艺装备的自动化水平。 (4) 发展检测仪器。检测水平在一定程度上反映了行业水平,在轴承行业应发展高效、精密适合于自动线使用的主动测量和线外专项自动检测仪器。 (5) 开展复合磨削研究工作。复合磨削具有合并加工工序减少装夹次数、提高加工精度的优点,因此,国外不少磨床都具有合并加工工序的功能,为赶上国际水平,必须开展这方面研制工作。滚动轴承滚动体制造技术1 钢球加工 钢球在球轴承中是承受载荷并与轴承的动态性能直接相关的零件。钢球的加工工艺应首先满足其成品标准要求,还应使钢球成品在在轴承元件中具有尽可能高的寿命、低的噪声、小的摩擦力和高的可靠性。钢球的加工工艺相对成熟。目前国内钢球制造工艺的原理和方法差异不大,工艺流程大体都是:原材料检查-钢球毛坯制造(冷、热镦,冷热轧制)-光球-热处理-硬磨-强化处理-初研-精研-清洗-检查-涂油包装。归于毛坯制造过程,一般直径在1英寸(4mm)以下的钢球采用冷镦工艺,直径在1英寸以上2英寸以下的采用热镦或热轧,直径在2英寸以上的采用车削或热锻。 工艺过程中,较明显的变化时采用光球工艺取代锉削、软磨工艺,虽然目前钢球的制造工艺过程与国外先进企业相似或相近,先进工艺也在逐步应用,但是整个行业发展很不均衡,特别是成形工序在生产效率、成型误差、产品总留量上都与先进水平有着较大差距,热处理和精研工序也有一定的差距。 钢球加工工艺的发展趋势主要集中在轧制工艺、树脂砂轮磨削工艺、钢球表面强化处理、热处理自动线加工和新型水剂研磨液的应用。1英寸以上钢球可采用轧制工艺。采用轧制工艺钢球尺寸精度高(一般可达05-09um)且无环带,材料利用率高(比冷镦可提高20%),生产效率高(能达到热镦的5倍),具有较高的强度和良好的尺寸稳定性,轧制球坯具有金属流线分布均匀,寿命长等众多优点,但轧辊设计制造比较复杂,轧辊材料成本较高。树脂砂轮磨研工艺,以磨代研对钢球进行终加工,能较稳定地提高钢球精度及表面质量,改善钢球的动态性能,特别是对降低振动值起到关键作用,同时对轴承合套异常声也有明显改善。用此技术加工钢球磨削均匀,克服了用铸铁盘研磨添加研磨剂不均匀而影响钢球质量的人为因素,同时树脂专用磨削液污染小,加工后的钢球表面易于清洗,且生产效率有较大的提高,大大降低了成本。2 滚子加工 理论上,滚子与滚道的接触是线接触,所以滚子承受的载荷较大,实际使用和试验均表明滚子是滚子轴承中最薄弱的零件,滚子的制造质量对轴承的工作性能(如旋转精度、振动、噪声和灵活性等)均有很大影响,是影响轴承使用寿命的主要因素。 我国滚子生产在滚子设计、工装设计、工艺编制和检测规程等各方面受传统模式的束缚,在设计思想和设计理念上存在差距,缺乏创新求变的意识,缺乏细致的研究和系统的综合分析。设备、工装、原材料、管理水平、工序质量控制能力受传统习惯的制约,导致滚子生产工艺路线长、加工留量大、加工遍数多、上下料次数多。生产设备陈旧、工装工具多年没有改进,生产工艺落后,原材料浪费,生产成本增加,工艺合理性差,滚子、滚针装备与工艺水平是轴承行业内较落后的。直径Φ24mm以下的圆柱滚子、圆锥滚子和调心滚子的毛坯成形基本上采用Z31-25、Z31-13冷镦机,采用盘料或直条料的开式切料,一次成形的形位公差和尺寸散差大,综合材料利用率低。后工序加工(硬磨)国内普遍使用M1080、XF004一般滚子专用磨床,就圆锥滚子而言,其产品加工精度一般达到JB/T10235规定的Ⅲ级精度质量水平。 国外先进的加工方法多为成行工序使用高速双击冷镦机成形,封闭切料,成形公差小,留量小,综合材料利用率高。例如直径小于32mm的滚子成形误差≤ 1mm,生产效率60-200次/min,Φ32mm以上时,采用车削成形加工。后工序加工(硬磨)采用高速高精度全自动磨床,产品质量水平在圆度误差、批直径变动量、圆锥角变动量的精度上与国内相比均提高1倍,表面粗糙度水平提高4倍以上,圆锥滚子综合精度稳定达到JB/T10235的Ⅰ级精度水平,SKF滚子已达到规定的0级水平。 对于圆柱滚子外径磨削,国产设备基本达到产品要求,但端面终磨和精研设备精度难于满足加工Ⅰ级滚子的要求,特别是端面跳动和表面粗糙度的要求距世界先进企业仍有较大差距。 按轴承行业“十五”规划目标,经新一轮的技术改造后,要求精密滚子到达Ⅰ级,稳定批量达到Ⅱ级,实现滚子设备标准化、工艺标准化、以及工装标准化。专业滚子生产覆盖率达50%,凸度化率达70%,外径超精普及化率达50%,球基面无磁磨削普及化率60%,圆锥滚子Ⅱ级精度以上达到60%,圆柱滚子Ⅱ级精度以上达到75%当前国滚子生产还不能完全达到这个要求,为了提高滚子质量,应尽快组织专业化结构调整,发展一批具有一定规模的专业化滚子生产骨干企业。推广新技术、新工艺、新装备、新的管理方法,完善和推广滚子联线加工工艺、对数曲线工艺、弧端面工艺、光饰工艺、喷丸加工工艺、可控气氛热处理工艺、表面强化工艺等,进一步扩大新型模具材料、磨削液、滚子清洗、退磁、干燥、涂油联线设备,滚子表面光饰机,滚子表面强化机及滚子高效喷丸处理机床的开发。
关于这方面研究的最新进展和相关的论文题目可以看下铭文网的,我的硕士小论文就是求助铭文网的老师搞定的,真的是非常效率加专业,很快就给我了,论文的修改过程也很顺利,投稿到录用来回只用了一个多月,比起同学发表的文章来说真的是超级速度了。
高强高导材料在机械、航空航天等行业有着极为广泛的用途,如电力机车受电弓、电磁发射装置轨道材料、电刷等,它们要求材料不仅具有高导电性,而且要具有较高的耐磨性。由于纯铜是传统的高导电材料,但其强度低耐热性差,大大限制了其应用范围。本文采用内氧化结合热挤压的方法制备出了高导电高耐磨性的Cu-La2O3复合材料,采用扫描电子显微镜(SEM)、透射电子显微镜(TEM)和X射线衍射分析仪(XRD)等微观手段,系统研究了载荷、滑动速度和电流等对Cu-La2O3复合材料摩擦磨损行为的影响,揭示了摩擦副的磨损机制,为高性能耐磨铜基复合材料的应用提供理论与实验依据。通过对不同La2O3含量的复合材料性能测试,系统研究了压制压力、烧结温度和增强体含量对材料物理性能和力学性能的影响。研究结果表明Cu-3wt%La2O3复合材料的硬度和导电率在900℃时达到峰值;当温度进一步升高时,由于烧结体内颗粒长大,使材料性能下降。随La2O3含量的增加,复合材料的硬度和拉伸强度升高,而导电率降低,当La2O3质量含量超过1%时,导电率低于80%IACS。对不同电流、载荷和速度条件下复合材料的摩擦磨损行为进行了研究。载流条件下,磨损率均随载荷的增加出现先降低而后增加的“U”型变化趋势。随着滑动速度的增加,最佳载荷相应的降低,此现象未见文献报道。电流、速度、载荷和距离等的综合作用使基体材料软化,磨损损失增大。Cu-La2O3复合材料在低载荷,高滑动速度和电流条件下的磨损形貌以电弧烧蚀、液滴飞溅和塑性变形为主要特征。在摩擦热、焦耳热及电弧热的共同作用下接触区内的接触点熔融甚至蒸发,并在摩擦副之间发生材料转移。磨损过程为氧化磨损、磨粒磨损、粘着磨损、疲劳磨损和电弧烧蚀等多种磨损机制共同作用的结果。研究了Cu-La2O3复合材料的高速摩擦磨损行为。结果表明:随着La2O3含量的增加,复合材料的磨损率降低。La2O3的加入不仅提高了复合材料的耐磨性,而且延缓了严重磨损的发生。在复合材料的轻微磨损阶段,机械混合层的形成与部分破裂导致的氧化磨损和磨粒磨损为主要的磨损机制;在严重磨损阶段,剥层磨损和粘着磨损成为主要的磨损机制,复合材料磨损表面具有划痕、塑性变形、粘着等主要特征。磨损过程包括材料转移、亚表层塑性变形及磨屑与磨损表面的机械混合等。研究了机械混合层对复合材料摩擦磨损行为的影响。结果发现:机械混合层的形成率和断裂率决定了复合材料的磨损行为,它存在于整个的轻微磨损阶段。随着载荷的增加,机械混合层的硬度和厚度均增大。不同La2O3含量的复合材料其磨损率发生突变的临界载荷随着机械混合层厚度的增加而增大,但随机械混合层硬度增大而减小,硬度大而薄的机械混合层具有大的转变载荷。研究了真空及低温条件下Cu-La2O3复合材料的摩擦磨损行为。随着滑动距离的增加,首先摩擦系数急剧升高出现摩擦系数的最高值,而后降低并在一定的范围内波动。随着载荷的增加,不同滑动速度下的磨损率均呈现出增加的趋势。当超过一定的滑动速度时,磨损率将发生突变,且随载荷的增加,发生突变所对应的速度减小。Cu-La2O3复合材料在真空中的磨损机制主要为粘着磨损。复合材料磨损表面具有犁沟、塑性变形和粘着等特征。轴承钢上存在大量的粘着转移物,形成明显的材料转移层,在真空磨损过程中,复合材料与转移层之间存在材料间的相互转移。